De la fumée des locomotives à vapeur aux trains modernes : la maintenance, enjeu majeur des exploitants ferroviaires, s’équipe, se modernise, en un mot s’améliore !
Aujourd’hui : une maintenance d’anticipation
Une meilleure préparation grâce à des données plus riches
Le maître mot de la maintenance actuelle, c’est l’anticipation. Pour préparer la maintenance, on doit analyser en temps réel les données venant des trains. Pour analyser les données, on doit mesurer, donc équiper et connecter les trains.
Les rames modernes sont équipées de capteurs pour surveiller l’état des fonctions (moteurs, portes, captages de la tension, etc.).
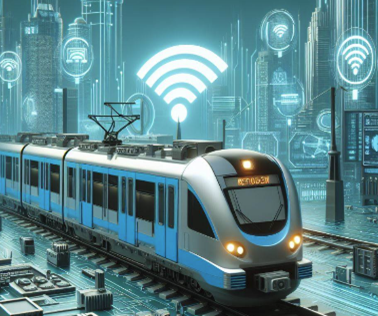
Les outils digitaux sont au service de la « maintenance 4.0 »
C’est ici qu’entre en jeu la maintenance 4.0, dont on peut citer les technologies clés :
L’Internet des objets (IoT) permet de collecter des données en temps réel sur l’état des équipements.
Le big data permet d’analyser les données collectées pour identifier les tendances et les anomalies.
Télédiagnostic : les rames sont de plus en plus communicantes et permettent grâce à des données fournies en temps réel, de détecter très rapidement des indices de pannes.
La GMAO (gestion de maintenance assistée par ordinateur) collecte toutes les données, et permet, avec une version mobile (sur tablette par exemple), de réaliser la maintenance partout.
Des nouvelles missions apparaissent chez les opérateurs ferroviaires, notamment les ingénieries chargées de programmer les modèles d’analyse, et les opérateurs de surveillance de l’état technique chargés d’anticiper les pannes ou d’en atténuer les conséquences.
La norme européenne ECE (Entité en Charge de l’Entretien) prescrit d’ailleurs une organisation dans ce sens.
Un exemple pour mieux comprendre : une panne évitée sur une porte
Une porte d’accès dans un train se ferme de plus en plus lentement depuis quelques jours.
Les données indiquent que le temps de fermeture est toujours correct, mais l’analyse de l’évolution de la vitesse permet de prévoir une panne dans 8 jours.
L’opérateur chargé de la surveillance de l’état technique reçoit automatiquement une alerte et génère un ordre de travail dans la GMAO. L’ordre de travail est pris en compte par le site de maintenance, et planifié.
Les ressources pour réaliser la maintenance sont réservées automatiquement : pièces (le moteur de la porte), installations, outillages, opérateurs de maintenance compétents…
Le jour J, la maintenance est réalisée : la porte est réparée avant la panne.
Le train repart en service commercial, le problème de porte n’a eu aucun impact sur les voyageurs.
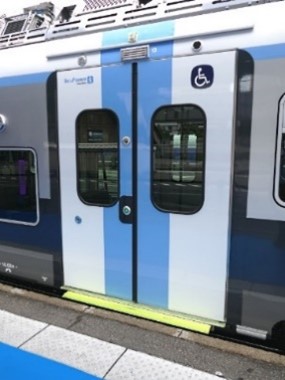
Souvenons nous : le temps de la vapeur !
Un plan de maintenance fixe et des signalements humains
La maintenance d’avant est basée sur un plan de maintenance préventive fixe : chaque opération est réalisée à une fréquence donnée en fonction du kilomètre parcouru ou d’un temps donné.
Les conducteurs ont une grande part de responsabilité dans la maintenance : en général issus des ateliers de réparation, ils peuvent évoluer au cours de leur carrière comme chauffeurs (alimentation de la chaudière) puis mécaniciens (conduite et entretien en ligne).
L’équipage touchait du charbon (du vrai charbon, puis plus tard de l’argent : la fameuse prime de charbon, disparue en 1970). Plus les conducteurs étaient « économes », plus ils pouvaient garder de charbon pour leur usage personnel : oui, on parlait déjà de rémunération à l’objectif et d’écoconduite à l’époque !
Les conducteurs étaient donc très sensibles à toute anomalie constatée : c’est la maintenance corrective, basée sur les signalements humains. Emile Zola le raconte dans « La bête humaine », le mécanicien Jacques et sa locomotive Lison : « Pendant que le foyer ronflait et que la Lison peu à peu entrait en pression, Jacques tournait autour d’elle, l’inspectant dans chacune de ses pièces, tâchant de découvrir pourquoi, le matin, elle lui avait mangé plus de graisse que de coutume. »
Dans les ateliers de maintenance, les documents (registres d’entretien) occupent une place importante, c’est la vie de chaque engin qui est formalisée sur papier (changement d’organes majeurs, opérations d’entretiens, visites, révisions, etc.).
Ces documents papier ne sont disponibles que dans un seul atelier : chaque engin a son atelier « référent ». En cas de changement d’atelier, le registre déménage avec son engin : pas facile pour accéder aux données !
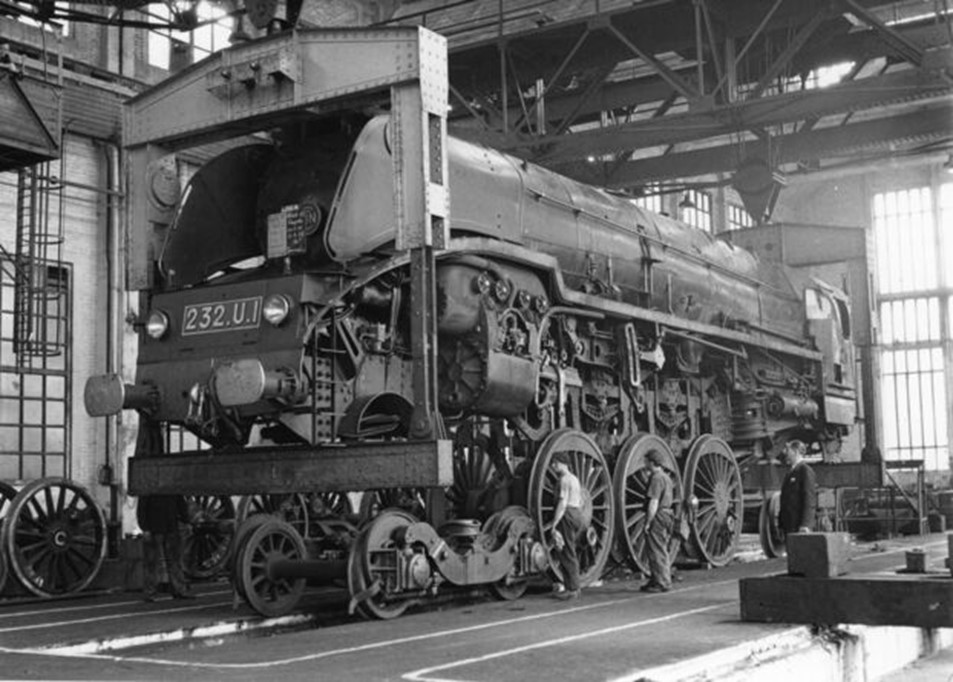
Retour dans le présent : des outils modernes à forte valeur ajoutée
Certaines nouveautés sont déjà mises en service pour mesurer et anticiper
Les outils Mobiles, comme les mesures Laser pour les roues et les disques de frein, fonctionnent et font gagner du temps par rapport aux mesures manuelles.
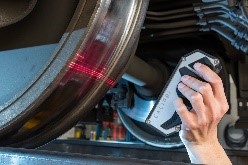
Les bancs automatisés1 permettent de mesurer des centaines d’éléments au passage d’une rame [CB1] en quelques minutes, contre quelques heures avec une intervention humaine.
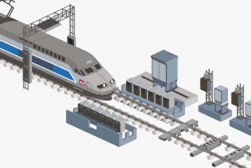
Quelques nouveautés à stabiliser :
Les drones : aujourd’hui ils sont utilisés pour la maintenance du réseau ferroviaire, moins pour les matériels roulants.
IA (intelligence artificielle) / Prédictif : Ce sont actuellement essentiellement des modèles statistiques et des équations qui sont utilisées pour anticiper les pannes, mais l’heure de l’IA viendra !
Réalité augmentée : elle permet à un expert de se projeter en immersion dans un train en panne grâce à un opérateur qui porte des lunettes connectées. Ce concept peut permettre une proximité entre le terrain et l’ingénierie, mais attention : la maintenance se passe souvent de nuit.
Et demain ?
Une maintenance ferroviaire préparée dès la conception du train
La maintenance des nouveaux trains sera prévue dès la conception de la fabrication :
- Des capteurs montés sur les organes clés dès la fabrication
- Des données plus riches
- Une connectivité accrue pour une meilleure réactivité
- Des analyses plus poussées pour anticiper tous les indices de panne
- Une meilleure accessibilité des organes pour les opérateurs, prise en compte des retours d’expériences sur les trains en circulation…
Comme beaucoup de secteurs, la maintenance ferroviaire tire profit des nouvelles technologies. Les investissements étant conséquents, le risque est d’avoir une maintenance à 2 vitesses, en fonction du budget des exploitants ferroviaires.
Gageons que ces améliorations seront standardisées et permettront une fiabilisation globale du système ferroviaire !
1 : https://numerique.sncf.com/actualites/des-bancs-automatises-pour-revolutionner-la-maintenance-des-trains/